In the construction field, the quality of sealants is crucial as it directly relates to the waterproofing, sealing effectiveness, and overall structural stability of buildings. Tensile adhesion performance, a key mechanical property indicator for measuring sealant quality, covers aspects such as tensile strength, maximum tensile elongation at break, and adhesion. Among these, tensile strength directly reflects the sealant's ability to withstand loads, which is extremely important for silicone structural sealants. The maximum tensile elongation at break reflects the elasticity of the sealant and is closely related to its displacement resistance, making it an important indicator that cannot be ignored in the development of building joint sealants.
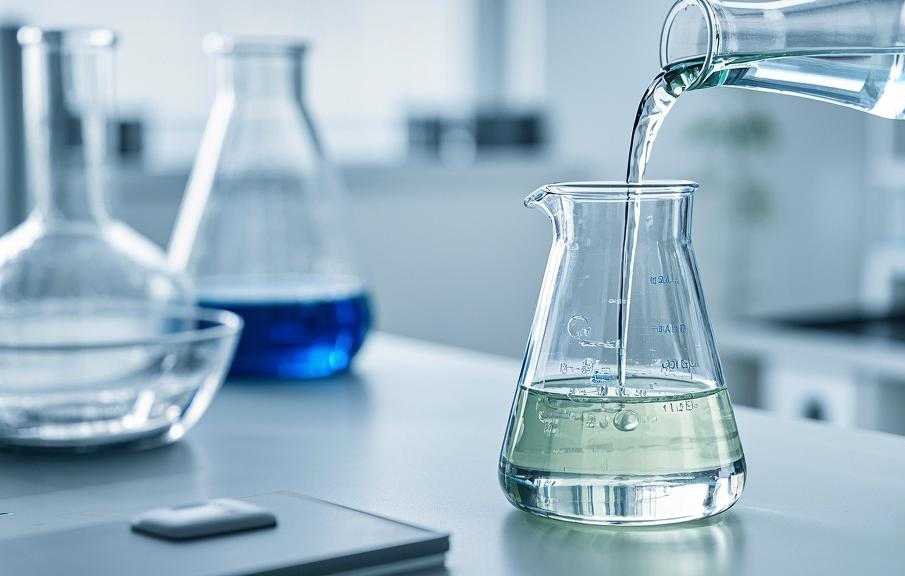
The tensile mechanical properties of sealants are mainly achieved through two approaches. On one hand, the main polymer of the sealant (107 adhesive) and the cross-linking agent react and cure into an elastomer by absorbing moisture from the air under the action of a catalyst, thus endowing the sealant with certain mechanical properties such as strength and elasticity. On the other hand, to further enhance the mechanical properties of the sealant, fillers such as calcium carbonate and white carbon black are usually added for reinforcement, and plasticizers are added to improve the compatibility of the sealant system.
The Impact of Dimethyl Silicone Oil on Tensile Strength
As the content of dimethyl silicone oil increases, the tensile strength of the sealant shows a general downward trend. When the content of dimethyl silicone oil is 20%, the tensile strength retention rates of alcohol-releasing and ketone-oxime-releasing sealants are 98.6% and 94.5%, respectively. However, when the content of dimethyl silicone oil is in the range of 20% - 30%, the tensile strength of both alcohol-releasing and ketone-oxime-releasing sealants decreases significantly. Especially when 30% dimethyl silicone oil is added, the strength retention rates of both types of sealants have dropped to less than 90%. It should be noted that there is no significant difference in the impact of dimethyl silicone oil on the tensile strength of alcohol-releasing and ketone-oxime-releasing sealants.
The Impact of Dimethyl Silicone Oil on Maximum Tensile Elongation at Break
It can be observed from Figure 1-b that as the content of dimethyl silicone oil increases, the maximum tensile elongation at break of the sealant shows an overall upward trend. When the content of dimethyl silicone oil is 20%, the maximum tensile elongation at break of alcohol-releasing and ketone-oxime-releasing sealants reaches 358% and 374%, respectively, which is an increase of 62.7% and 16.9% compared with the products without dimethyl silicone oil. However, when the content of dimethyl silicone oil exceeds 20%, the increase in the elongation at break of both types of sealants tends to be gentle. Comparing the elongation data of alcohol-releasing and ketone-oxime-releasing sealants, the effect of dimethyl silicone oil on the elongation of alcohol-releasing sealants is more significant, but the overall trend of the two basically remains consistent.
Recommendations for the Content of Dimethyl Silicone Oil
Based on the above analysis, in order to ensure the comprehensive mechanical properties of sealants and to give full play to the role of dimethyl silicone oil as a plasticizer and diluent, it is recommended that the content of dimethyl silicone oil in the actual sealant formula design should be controlled within the range of no more than 20%. This content range can effectively improve the elasticity of the sealant without significantly affecting its tensile strength, thereby ensuring the reliability and stability of the sealant in practical applications.